FRP Chemical Lining
Fiberglass Reinforced Plastics (FRP) lining is protective lamination on the desired surface (RCC, MS, WOOD, PLASTICS, etc.) to provide corrosion resistance against water, chemical proofing, high strength, dimension stability, and is known for its ease of application, maintain, and repair.
FRP lining is widely used in chemical industries for atmospheric corrosion resistance, weatherproofing, water, chemical proofing, and to maintain the purity of the material stored inside the containers. Further, FRP lining is used for repair and maintenance of wide range of RCC, construction like over head storage tanks, pipe lines, building construction cracks, water/ chemical proofing, bridges & flyover constructions cracks etc. which provide not only corrosion resistance but also high strength and dimension stability at low cost and ease of application.
The desired reinforcement is given by use of fiberglass, which is available in various ranges and is applied as per requirement and utility. Ranges of fiberglass reinforcement are – CSM, Woven Roving, and Surface mat, Honeycomb mats. For corrosion resistance, water, chemical proofing wide range of resins like Isopthalic, Bisphenol, Vinyl Ester etc. are available and is applied as per requirement.
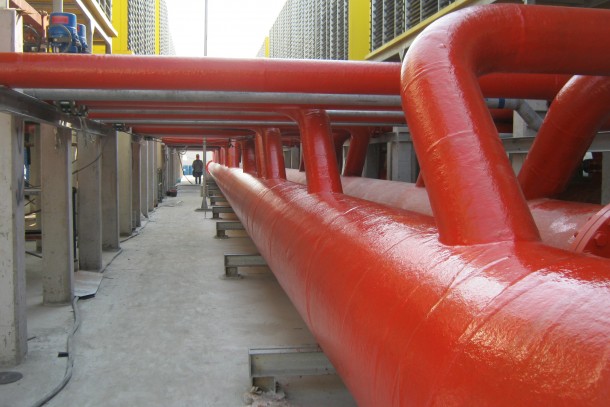
Raw Material used in FRP Lining
1.Glass Fiber–confirming to IS-11551-1986
2.Glass Fiber Rovings-confirming to IS-11320-1997
3.Unsaturated Polyester Resin confirming to IS-6746-1994
4.Cobalt Napthanate (Accelerator)
5.MEKP (Methyl Ethyl Ketone Peroxide)-Curing Agents.
6.N.C Thinner – for cleaning and surface preparation.
Steps for FRP Lining
1. The desired surface to be lined is cleaned properly using iron paper, grinders or sand blasting as required and proper surface is prepared free of water, grease, foreign deposition etc. The surface is checked properly to ensure excellent bonding between the surface & the FRP lining.
2. Once the surface preparation is done, as required, resin coat is applied and allowed to cure. This coat should fill up all the pinholes and the damaged area of the surface.
3. After coating, as desired, fiberglass mat (CSM)- Chopped Strand Mat is then spread on the surface and is wetted with resin and properly brushed to ensure minimum air trapping and good bonding with the surface. Fiberglass layers are applied depending on the thickness to be given. The lamination is allowed to cure.
4. Once the lamination is cured immediately one layer of surface mat (veil) is applied as final layer followed by one resin rich coat of resin for better corrosion resistance.
5. During lining, precaution are taken for proper bonding and if required custommade arrangements are made like provision of inbuilt M.S/Wooden/aluminum stripe / pegs are provided.
6. Precaution is also taken at the time of surface finish as required and cracks; pits etc. are properly filled during surface preparation.
7. Good workmanship and supervision is of prime importance during execution of job, which needs technical and specialized workers to do the same.
8. FRP lining provides complete leak proofing, corrosion resistance, strength and very good life for virgin material lining as well as for old structures etc.